Hardware Systems
Focal Automation has the training and experience on a wide range of hardware systems for competent design, installation, configuration, programming, commissioning, start-up, and operational training.
Focal Automation hardware services include the following types of systems:
​
DCS Systems
Focal Automation is North America’s apex provider of DCS services. Typically, we are involved in a project during pre-feed to ensure the customer is integrating the correct control system based on current wants and needs with focus on: communications, budget, timeline, redundancies, safety requirements, licensing, future expansion and training. Once the correct system decision is established, we assist with the panel design and IO layout, control narratives, shutdown keys, logic and interface standards, programming, commissioning, testing, documentation and training.
We also provide management and engineering services to manage accountability, cost, schedules, forecasting, management of change and reporting.
Our Commissioning team includes but is not limited to; electricians, instrumentation technologists, FAT and SAT testing, control manuals, loop checks, narrative and shutdown key checks and a hand over package with backups and images of the control system from handover date. Our integrators take great pride in our operator and service technician training for all new and existing projects. Training can be scheduled in our Sherwood park, Calgary or Grande Prairie locations and at the customers preferred location.
​
-
ABB / Bailey
-
Honeywell
-
PlantScape
-
Moore APACs / Siemens
-
Delta V
-
Yokogawa
​
​
​
​
​
​
​
​
​
​
​
​
​
​
​
​
​
​
​
​
​
​
​
​
​
​
​
​
​
​
​
​
​
​
​
​
​
RTU & SCADA
An RTU (Remote Terminal Unit) is an individual device, or a collection of devices, that are installed in a remote site or location which monitors, controls and provides feedback of field devices. The RTU exchanges data between itself and a master unit or database via a wired or wireless (radio, satellite, microwave) communication link. The data being monitored can be analogue and/or digital depending on the field device/s in operation. Some industries that utilize RTU’s include mining, gas & oil, water treatment, agriculture and environmental.
​
An RTU is a microprocessor-controlled device which, in order to function as desired, must be programmed with specific software code. The code is a defined set of instructions that the RTU understands and executes as required. Any error or ‘bug’ in the code may cause the RTU, along with any device it communicates with, to malfunction. Prior to dispatch, RTUs are programmed using an external device such as a PC or laptop and generally require very little maintenance over their expected life.
​
In order for the RTU to receive and implement the correct set of instructions, the programmer must have knowledge of both the software requirements and hardware elements including the field and telemetry devices. RTUs can have their software parameters modified via the telemetry link; however this may affect some, or all, of the respective field devices, so it’s imperative that any upgrades are managed correctly.
​
Some common network connections, communication protocols and field devices used with RTUs include:
​
-
ModBus
-
CIP
-
RS232/422/485
-
HART
-
Ethernet/IP
-
Analog signals
-
Profibus
-
Canbus
​
To ensure the best RTU performance is achieved, especially when considering the remote nature of the installations and the cost associated with potential malfunctions, it is important that RTU programming is done by trained, qualified and experienced RTU engineers.
Focal Automation employs numerous expert RTU programmers and engineers and measurement specialists, so can offer unmatched technical capabilities with the highest levels of service and support. To find out more about how Focal Automation expert RTU programming services can benefit your current or next project then contact us at any of our branches.
​
PLC/DCS ​
A very important first step to PLC and DCS development is to ensure the clients programming standards align with the developers. This step is established early on to ensure the client will be happy with the solution and that they will be able to maintain it for years to come. If the client doesn’t have a confirmed set of standards it is important that we review our standards and sign off approvals to manage expectations.
​
Engineering and IT Insight:
Develop a mental model to address real-time programming, which differs from web development or classical programming. Base real-time programmable logic controller (PLC) and distributed control system (DCS) programs on models of functional programming, encapsulation, hierarchy decomposition, and petri nets. Please do not accept unstructured and poorly designed PLC and DCS code, as it will cost you way more in the long haul. Use the following advice to improve programmable logic controller (PLC) and distributed control system (DCS) programming. Real-time control system programming is really programming, but it uses languages and models that are not normally taught in programming classes.
The real-time languages and models also do not have much in common with modern programming languages such as C#, Java, PHP, Perl, and Python. When writing control programs, engineers and programmers usually have to relearn how to approach problems using either Function Block Diagram programming when working on DCSs or the IEC 61131-3 languages when working on PLCs.
All of Focal Automations engineers and specialists have spent years mastering these languages for development of bumpless, alarm managed, smooth processes and sequences.
​
-
Omron
-
Allen Bradley
-
Modicon
-
GE Fanuc
-
Horner
-
Honeywell
​
​
Flow Computers
A flow computer is a specialized type of computer that uses complex calculations to interpret the data from flow meters and to calculate and record the volume of a particular flowing substance at a particular point in time. Flow computers can be used for gases or liquids and are in demand across various industries. For most accurate and consistent results, flow computers should possess sophisticated programming, a user-friendly interface and damage-resistant hardware components.
Flow computers are programmed with the necessary algorithms and equations needed to accurately interpret the data from flow meters and other flow measuring devices. Many manufacturers make flow computers that can be connected to a variety of devices including liquid provers, gas chromatographs, distributed control systems and more.
​
​
​
​
​
​
​
​
​
​
​
​
​
​
​
​
​
​
​
​
​
​
​
​
​
​
​
​
​
​
​
​
The first task of the flow computer is to record the continuous stream of data. The second task is to continuously analyze the data received and use it to transmit a report of the current attributed of the measurable fluid or gas at fixed points in time. Users can configure their computers to create records at particular times or for specific intervals. For example, a flow computer can create a record of the volume of flow every hour, on the first of the month, or on a batch basis. Flow computers can be extremely accurate, but only with proper maintenance and calibration. The more sophisticated a flow computer is, the more capable it is of processing increasingly incremental data points and the more input sources it can handle. Some flow computers can simultaneously process running data from several meters.
​
-
Omni
-
Spirit IT FlowX
-
ROC
-
Bristol
-
Micromotion
-
SCADApack
-
Barton
​
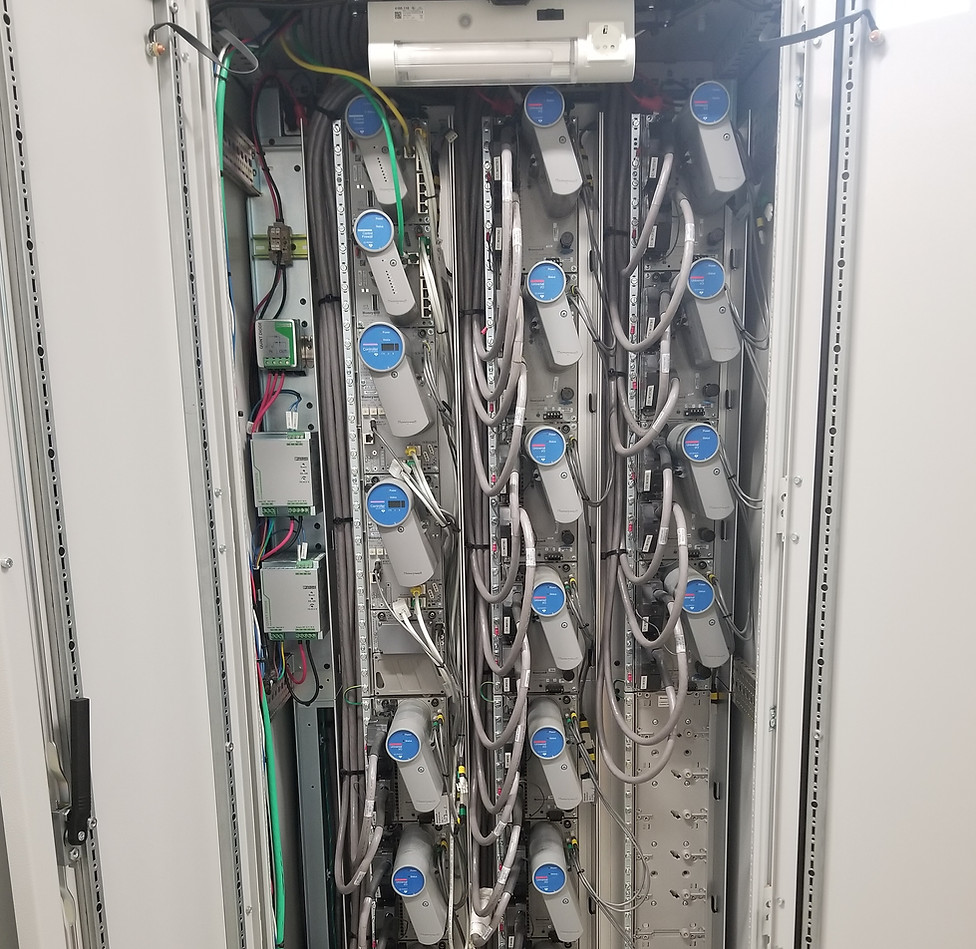
